Imagine a colossal gold mine, Australia’s largest no less, where its scale and longevity could be confused for an iron ore mine in the Pilbara. Where massive trucks navigate the landscape with uncanny precision, devoid of almost all human drivers. This isn’t science fiction; it’s the reality at Boddington, a mine that has rewritten the rulebook on gold mining best practices in autonomous haulage and is paving the way for future rollouts across Newmont’s portfolio.
Boddington’s drive for efficiency, safety and sustainability and lessons for the future
I was fortunate enough to recently visit Newmont’s Boddington Gold Mine (BGM), located some 120km south-east of Perth. For 16 years under Newmont’s management, Boddington has been a consistent gold producer at scale, churning out copper-gold concentrate and gold bars. Newmont has mine life extension plans that could see the BGM operation extend to 2059. Currently, Newmont mines from the astutely named North and South pits, but by the end of the mine’s life, the pit design would eventually merge into one, rivalling Kalgoorlie’s world-renowned Super Pit.
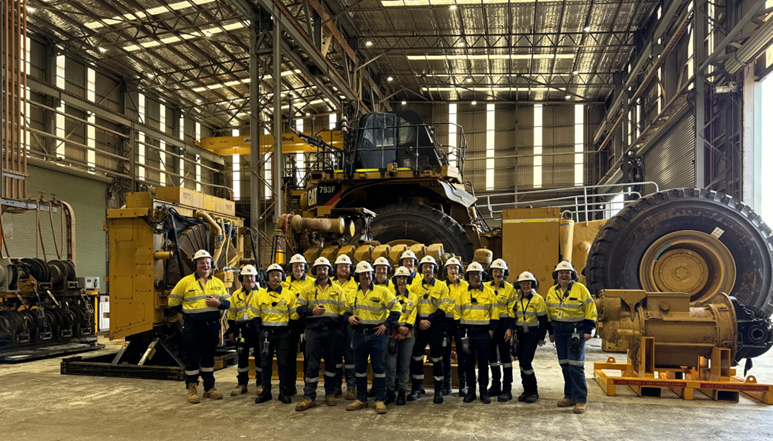
Source: Tyndall AM, March 2024.
A Pioneering Journey: The rise of AHS at Boddington and the learnings
Boddington’s Autonomous Haulage System (AHS) journey is a story pushing the boundaries of both productivity gains and ESG standards. With a fleet of 41 CAT 793F trucks, these behemoths are guided by the sophisticated CAT MineStar operating system. Launched in 2021, this system has propelled Boddington to the forefront of mining technology, making it the world’s first open-pit gold mine to boast a fully autonomous haulage fleet. The US$150 million project to convert the legacy fleet was completed ahead of schedule and under budget, even amidst the disruptions of COVID-19.
The AHS roll out encountered several challenges during its commissioning phase including in-pit communications issues, severe weather and heavy rainfall, shovel reliability issues and issues managing in-pit bench hygiene. These obstacles provided valuable learning opportunities through commissioning. Key learnings from the roll out have been focused on optimising the mine plan design to best suit the operating conditions of the AHS fleet, such as straightening roads and removing intersections. AHS trucks abide by a set of strict rules that ensure a predictable and safe outcome. These rules include slowing down at intersections and around bends and when coming into proximity with light vehicles. Additionally, meticulous road maintenance and assessing ramp gradation became crucial for the improved operations.
It is believed that 95% of learnings from Boddington can be replicated across future AHS fleet roll outs at other assets (discussed later). Many of the learnings are also applicable to non-AHS fleet with the issues identified by AHS fleet communicated to Newmont’s other open pit operations.
Justifying the investment: Outcomes witnessed to date and the benefit of a systematic approach
After 13 years of 100% Newmont ownership, it took the AHS fleet only 12 months to beat the tonne per kilometre of movement performance record by 10%. Under the company’s roadmap (refer Figure 1), management believes there is another 10% of productivity upside available. These productivity improvements will be achieved via a combination of improved truck availability (reduced downtime) and increased tonnes per kilometre.
The benefits of AHS extend far beyond mere operational efficiency, with safety taking centre stage by removing human interactions with large and heavy machinery. Human error is significantly reduced as a result of autonomous trucks meticulously following designated paths and operating parameters. Critically, this translates to a dramatic decrease in the risk of fatalities and vehicle collisions.
Figure 1: Newmont’s full potential productivity potential roadmap
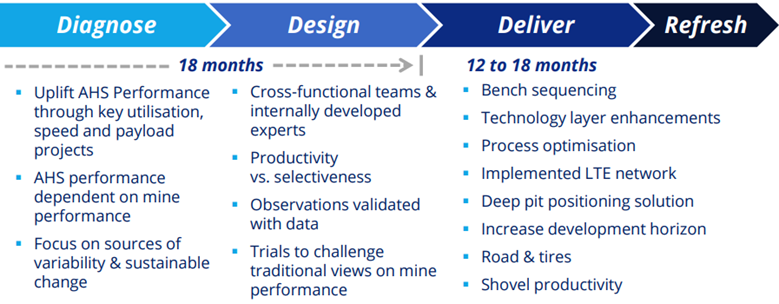
Source: Boddington, March 2024.
The environmental benefits are undeniable. Reduced fuel consumption due to optimized operations translates to lower greenhouse gas emissions. Since the introduction of the AHS, the Boddington operation has achieved significant fuel efficiency, saving approximately 1.5 million litres per year. Additionally, less wear and tear on tyres and other consumables contribute to a more sustainable mining operation.
The financial and productivity improvements – alongside the improvements in safety – boil down to operating discipline. Human operators compensate when the mine plan or operating conditions are not optimal, making it very hard for managers to identify issues and correct appropriately. Autonomous trucks strictly adhere to all operating constraints, so when an issue is encountered, the system will alert operators in control and the truck will stop operating. This results in bottlenecks being identified and rectified more rapidly than when humans operate trucks.
For example, if the optimal path from the pit floor to the crusher is blocked due to poor bench hygiene, the human operator, depending on factors like KPIs and mine culture, could choose a longer route and leave the rectification of the optimal route outstanding. However, the autonomous truck fleet will flag this issue with control and the optional route will be restored, leading to savings on future diesel consumption and increasing productivity.
A future powered by AHS: Further opportunities within the Newmont portfolio
The potential applications of Boddington’s AHS learnings are vast. The ability to remove workers from hazardous environments and improve production efficiency makes AHS a compelling proposition across some of Newmont’s core assets. Underground mining operations at Cadia and Lihir are prime candidates for this technology. The Lihir ore body, for example, sits within an extinct volcano where ground temperatures can reach up to 80 degrees celsius. Regular geysers can erupt, making it too dangerous for humans to walk the pit floor, providing a significant opportunity for better remote operated technologies.
ESG benefits of AHS offers improved risk adjusted outcomes
AHS rollout is just one tool in the toolbox to realise latent operational value from a financial and ESG standpoint, while decreasing the risk of a material safety event occurring and offering improved risk adjusted returns. The benefits of deploying AHS are clear; it can reduce operating costs, reduce fleet maintenance and improve productivity alongside improving safety, all of which align with the ethos of responsible and sustainable mining practices.
Other Tyndall portfolio companies are also championing autonomous solutions, including Rio Tinto and BHP. At Tyndall, we analyse these metrics in absolute, relative, and directional trend terms, with safety metrics critical factors in both our assessment of the investable landscape and portfolio construction process.